Comprehensive Guide: What is Porosity in Welding and Just How to Prevent It
Comprehensive Guide: What is Porosity in Welding and Just How to Prevent It
Blog Article
The Science Behind Porosity: A Comprehensive Overview for Welders and Fabricators
Comprehending the detailed mechanisms behind porosity in welding is vital for welders and fabricators striving for impressive craftsmanship. From the structure of the base products to the intricacies of the welding process itself, a wide range of variables conspire to either worsen or ease the existence of porosity.
Recognizing Porosity in Welding
FIRST SENTENCE:
Examination of porosity in welding reveals essential understandings into the honesty and high quality of the weld joint. Porosity, identified by the visibility of tooth cavities or gaps within the weld steel, is a typical worry in welding procedures. These voids, if not appropriately attended to, can jeopardize the architectural stability and mechanical residential properties of the weld, leading to prospective failures in the completed item.
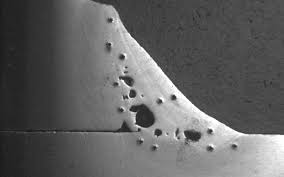
To spot and quantify porosity, non-destructive screening methods such as ultrasonic testing or X-ray inspection are typically employed. These techniques enable the recognition of interior defects without endangering the integrity of the weld. By analyzing the size, form, and distribution of porosity within a weld, welders can make enlightened choices to boost their welding processes and achieve sounder weld joints.
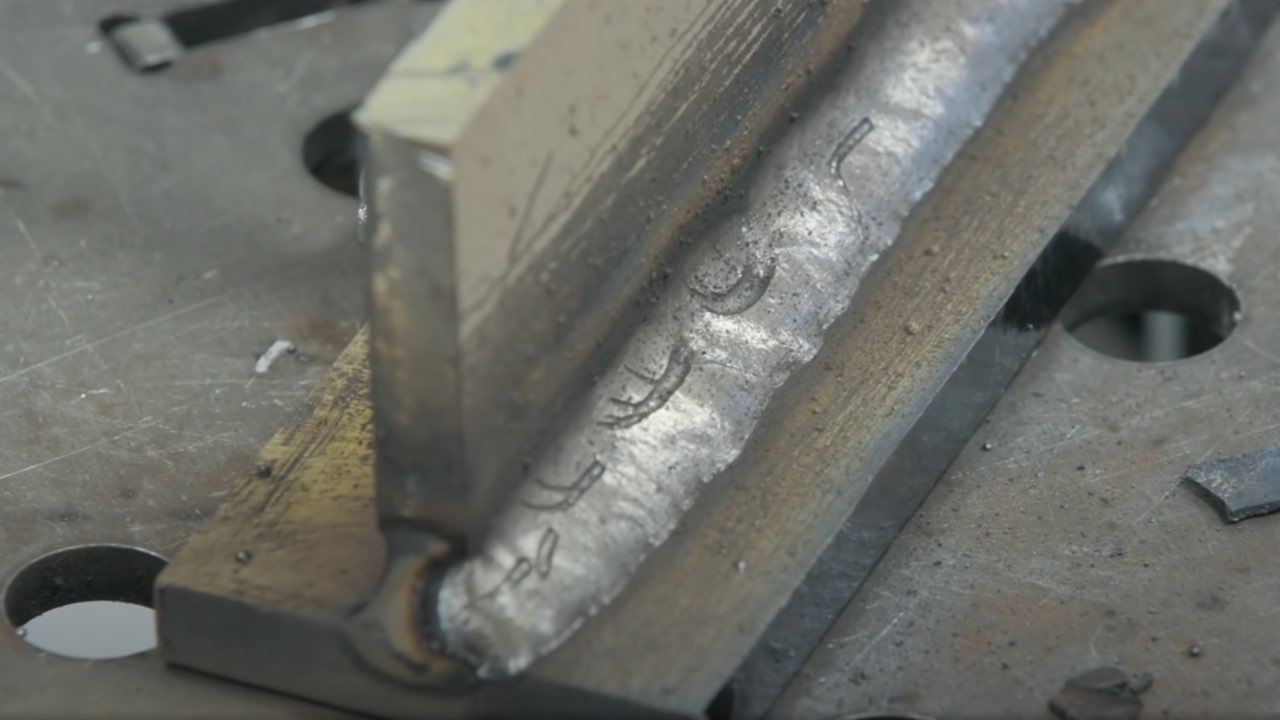
Variables Affecting Porosity Development
The incident of porosity in welding is affected by a myriad of elements, varying from gas securing effectiveness to the complexities of welding specification setups. Welding specifications, consisting of voltage, present, travel speed, and electrode type, additionally influence porosity development. The welding technique used, such as gas steel arc welding (GMAW) or secured steel arc welding (SMAW), can affect porosity formation due to variants in heat circulation and gas insurance coverage - What is Porosity.
Impacts of Porosity on Weld High Quality
The existence of porosity also damages the weld's resistance to deterioration, as the entraped air or gases within the gaps can react with the my explanation surrounding setting, leading to deterioration over time. In addition, porosity can impede the weld's capability to endure pressure or influence, further threatening the general top quality and dependability of the welded framework. In important applications such as Visit This Link aerospace, automobile, or structural constructions, where security and durability are extremely important, the harmful results of porosity on weld quality can have extreme consequences, emphasizing the significance of lessening porosity via correct welding methods and procedures.
Methods to Decrease Porosity
Furthermore, making use of the suitable welding parameters, such as the proper voltage, current, and travel speed, is vital in avoiding porosity. Preserving a regular arc length and angle throughout welding likewise aids minimize the likelihood of porosity.

Moreover, picking the ideal shielding gas and keeping proper gas flow rates are important in reducing porosity. Using the suitable welding method, such as back-stepping or employing a weaving movement, can additionally aid disperse heat evenly and decrease the opportunities of porosity development. Finally, guaranteeing proper ventilation in the welding setting to remove any type of prospective resources of contamination is vital for accomplishing porosity-free welds. By carrying out these techniques, welders can effectively decrease porosity and create high-quality bonded joints.

Advanced Solutions for Porosity Control
Implementing innovative innovations and innovative methods plays a critical function in accomplishing premium control over porosity in welding processes. Additionally, using sophisticated welding strategies such as pulsed MIG welding or modified atmosphere welding can likewise assist mitigate porosity problems.
One more advanced remedy entails using innovative welding tools. Utilizing devices with integrated functions like waveform control and innovative power resources can improve weld quality and minimize porosity threats. The implementation of automated welding systems with precise control over criteria can significantly lessen porosity defects.
Moreover, including sophisticated surveillance and assessment innovations such as real-time X-ray imaging or automated ultrasonic screening can assist in spotting porosity early in the welding procedure, enabling instant rehabilitative activities. In general, incorporating these innovative services can considerably enhance porosity control and improve the overall top quality of welded her response components.
Final Thought
In verdict, recognizing the scientific research behind porosity in welding is crucial for welders and makers to create premium welds - What is Porosity. Advanced solutions for porosity control can further improve the welding procedure and make certain a solid and dependable weld.
Report this page